Улучшение трибологических свойств силицированного графита с помощью иерархически гибридного композита SiC/C
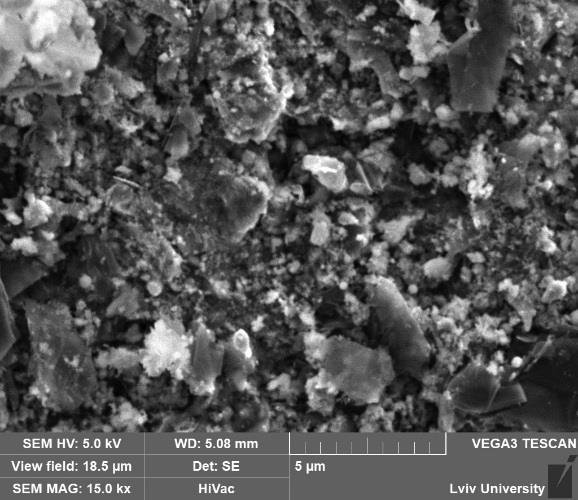
Композитные материалы SiC/C все более востребованы в передовых отраслях промышленности благодаря их высокой удельной прочности, высокой твердости, высокой жесткости, износостойкости и стойкости к окислению , а также низкому коэффициенту теплового расширения . Иерархически гибридные композиты SiC/C могут быть многообещающими кандидатами для применения в качестве материалов для подшипников качения, особенно обеспечивая меньшее проскальзывание на высоких скоростях. Поэтому трибологические свойства композитов во многом определяют качество и точность подшипникового узла при трении в условиях эксплуатации.
В трибологических испытаниях использовали два разных источника силицированного графита. Одним из них был материал российского обозначения СГ-П-0,5, который был получен методом осаждения кремния из паровой фазы при температуре 1800–2200 °С с внедрением в подложку из пористого графита. Он состоит из графита, карбида кремния и свободного кремния, при этом объем карбида кремния составляет 50–55 %, свободного кремния — 20 %, а остальное — свободный графит, что составляет около 30 %. Образцы СГ-П-0,5 для этого испытания были взяты из обслуживаемых подшипников с водяной смазкой. Основные физические свойства образцов СГ-П-0,5 и БСИ SiC-композитов представлены в табл. 1 .
Образец | Плотность г/см 3 | Прочность на растяжение, МПа | Прочность на сжатие МПа | Прочность на изгиб МПа | Модуль сжатия МПа |
Теплопроводность
Вт/(м · К) |
---|---|---|---|---|---|---|
СГ-П-0,5 | 2.4–2.6 | 60 | 420–450 | 100–120 | 1.27 × 105 | 120–140 |
БИС SiC | 2.65 | 50 | 412–441 | 190 | 1.40 × 105 | 150–175 |

Другим материалом был графит, пропитанный кремнием, полученный методом пропитки жидким кремнием (LSI SiC). Процедура следующая, обжиг при температуре 1500°С, температура плавления кремния 1414°С в течение 30 мин в вакуумной атмосфере. Образовку углерода засыпали в кремниевый порошковый слой в графитовом тигле с крышкой в высокотемпературной печи. Для получения однородной ванны жидкого кремния в углеродном образце образец в печи нагревали на 100% мощности до достижения заданной температуры.
После изготовления поверхностный остаточный кремний был смыт плавиковой кислотой , а слабая адгезия SiC удалена. Карбид бора использовался в качестве абразива для полной шлифовки перед испытанием на трение, чтобы гарантировать, что поверхности двух материалов имеют одинаковую шероховатость Ra 0,05. Ультразвуковую очистку проводили с использованием ацетона после измельчения.
Следует отметить, что выбор температуры реакции обусловлен тем, что фаза Si может полностью находиться в жидком состоянии выше температуры 1404 ± 5 °C, как показано на фазовой диаграмме Si–C на рис. 1 , где Si-фаза может полностью реагировать с образованием композитов SiC.
Трибологические испытания проводились в конфигурации «штифт на диске» на мультиобразцовой испытательной системе UMT-3 (Bruker). В частности, для встречного шлифования одного и того же материала в условиях погружения в воду и в сухом состоянии использовался измеритель трения и износа в контролируемой среде . В каждом испытании на верхний зажим помещался цилиндр диаметром 3 мм. Нижний образец крепился непосредственно к основанию в камере. Материал штифта цилиндра был таким же, как и у нижнего образца. Рабочие условия, применяемые для каждого испытания на трение, были следующими: нормальная сила (F N ) 10 Н и 40 Н, скорость вращения 100 об/мин, радиус инерции.составлял 15 мм, а продолжительность 30 мин в каждом тесте. Все испытания проводились при комнатной температуре на воздухе. Для каждого условия испытаний было проведено три испытания, чтобы проверить воспроизводимость результатов. COF измеряли и регистрировали во время теста на скольжение. Скорость износа рассчитывали по формуле, предложенной Archard et al.
куда Vi это объем износа.Vi=M/p, которая представляет собой отношение потери веса материала к плотности.Fn это нормальная нагрузка.это расстояние трения.

После трибологических испытаний образцы были разрезаны на круглые ломтики диаметром 50 мм и толщиной 5 мм с помощью проволочной электроэрозионной обработки . Микроструктурную характеристику изучали с помощью сканирующего электронного микроскопа (СЭМ, Zeiss Gemini SEM 300) с детектором энергодисперсионного спектрометра (ЭДС), работающего при ускоряющем напряжении 10 кВ, рабочем расстоянии 5–10 мм. Для идентификации компонентов, содержащихся в материалах, также использовались рентгеновская дифракция (XRD) и рамановский анализ.
Для обработки сканированных изображений, полученных с помощью СЭМ, использовался метод выделения признаков. В этом исследовании для извлечения особенностей изображений использовался алгоритм пороговой обработки Оцу, поскольку разные уровни серого представляли разные элементарные компоненты в режиме дифракции обратно рассеянных электронов (BSD) в электромикроскопе. Применение выделения признаков изображения к изображениям РЭМ в материаловедении было показано в качественных и количественных исследованиях. Чоудари и др. использовали качественные алгоритмы, такие как бинаризация, порог Оцу, маркировка связанных признаков и эрозия, при расчете наиболее характерных патологических параметров. Работа Раймундо и др. показали использование алгоритмов, таких как отключение морфологических операторов, диморфизма и меток признаков. Была выбрана конкретная блочная кватернизация , потому что несколько разных областей в образце варьировались в разных фазах для идентификации, включая SiC, Si и графит, особенно по сравнению с общим методом определения порога Оцу, таким как блочная бинаризация. Вычисляя межклассовую дисперсию между заданной шкалой серого и объективами, можно разделить три или четыре области. Представленный алгоритм исключения может быть использован для удаления шумовых элементов. Наконец, необходимо подсчитать пиксели, содержащиеся в каждом значении признака.
В материале LSI SiC испытание на окисление было проведено после подготовки образца. Полированный образец подвергали оксидированию в высокотемпературной печи с выдержкой при 400 °С в течение 2 ч в атмосфере кислорода. На рис. 3 представлены спектры КР образца LSI SiC до и после окисления. До окисления на поверхности образца существовали свободный кремний и графит, тогда как после окисления весь кремний на поверхности превратился в диоксид кремния. Следует отметить, что испытание на окисление направлено на то, чтобы убедиться, что характеристики изготовленных композитов, поскольку стойкость к окислению является ключевым свойством поверхности LSI SiC. Кроме того, оксидные слои на поверхности образцов удалялись перед испытанием на трение.
На рис. 4 , а–г показаны морфологические характеристики образца LSI SiC в различных состояниях, включая окисленную поверхность, внутреннюю микроструктуру без полной инфильтрации, примитивную микроструктуру и единичное зерно матрицы. На рис. 4 а–б видно, что внутри появилось лишь небольшое количество зерен, тогда как в образце композита LSI SiC остальное составил графит. На рис. 4в однородные кубические зерна со средним размером зерна 3–30 мкм плотно распределены по поверхности образца LSI SiC-композита, особенно вокруг более крупного зерна на рис. 4г. Рис. 4д–е – исходные морфологические характеристики образца СГ-П-0,5. На неполированной поверхности на образце образовалась большая часть открытоячеистой микроструктуры. После обработки на поверхности царапин получена уплощенная микроструктура.

На рис. 5 показаны морфология SEM и картирование EDS образцов композита LSI SiC при нормальной нагрузке 40 Н после испытания на трение. Причина в том, что метод EDS можно использовать для идентификации различных элементов на поверхности образца. В элементном распределении Si и C на рис. 5 можно сделать вывод, что темно-серая область может быть графитом на сканированном изображении, а светло-серая область может быть компонентом смеси SiC и Si. Таким образом, можно получить карту распределения для оценки различных элементов на поверхности. Кроме того, морфология композита LSI SiC в условиях сухого воздуха показала множество ямок с максимальным диаметром 100 мм на рис. 5а , тогда как при погружении в воду не было обнаруженоусловия. Эти ямки могут быть индикатором фреттинг-износа , который может привести к выпадению встроенного графита в сухих условиях во время процесса трения.

На рис. 6 показано сравнение материала СГ-П-0,5 до и после трибоиспытаний, в частности по распределению кислородного элемента до и после трения. При сухом трении на изношенной поверхности образца были небольшие царапины, тогда как при смазке водой поверхностные царапины не были очевидны . На рис. 6 а четкую границу в отображении элемента кислорода можно наблюдать между неизношенной и изношенной поверхностью образца. Это свидетельствует о окислении и износе межповерхностных поверхностей трущихся поверхностей во время трибологических испытаний.

В частности, в Таблице приведены удельные объемные доли элементов на поверхности образца при отображении ЭДС, особенно на изношенных/неизношенных участках после трибологического испытания. Можно обнаружить, что общее количество элементов было одинаковым для двух материалов. Разница может заключаться в том, что содержание кислорода значительно увеличилось после испытания на износ . Степень окисления в сухом состоянии была значительно выше, чем в состоянии со смазкой водой.
Элементарная доля поверхности до и после износа (об.%).
Элементы | СГ-П-0,5 | БИС SiC | ||||||
---|---|---|---|---|---|---|---|---|
Сухой воздух | Водяная смазка | Сухой воздух | Водяная смазка | |||||
Неизношенная поверхность | Изношенная поверхность | Неизношенная поверхность | Изношенная поверхность | Неизношенная поверхность | Изношенная поверхность | Неизношенная поверхность | Изношенная поверхность | |
А также | 13.48 | 13.16 | 13.62 | 16.74 | 20.32 | 16.33 | 14.69 | 15.27 |
С | 82.53 | 78.36 | 82.85 | 76.93 | 77 | 71.02 | 81.61 | 80.13 |
О | 3.64 | 8.12 | 2.88 | 6.14 | 2.35 | 12.23 | 3.43 | 4.32 |
Fe | 1.36 | 0.36 | 0.65 | 0.19 | 0.33 | 0.42 | 0.27 | 0.28 |
Постобработку полученного набора данных проводили с помощью недавно разработанной пользовательской программы в программном пакете Matlab. Извлечение признаков было выполнено на полученных изображениях SEM-BSE. Все полученные изображения SEM-BSE сначала были очищены путем удаления диких всплесков элементов. Затем на изображениях SEM-BSE были определены три градации серого, которые служили характеристическими значениями SiC, графита и фазы Si. Наконец, пороговое значение Otsu было использовано для классификации и регенерации компонентов фаз, представленных каждым цветом в градациях серого. Высокое разрешение сохранялось для фазовой реконструкции при постобработке данных.
На рис. 7 представлены изображения BSD и выделение признаков для образца СГ-П-0,5 и композита LSI SiC. Сканированное изображение BSD было разделено на три основные цветовые области в соответствии с различными уровнями серого, и, таким образом, компоненты в образце были идентифицированы методом EDS, где самая темная область может быть фазой графита, серая область - фазой SiC, а белая область. области в виде свободной фазы Si. Можно обнаружить, что в двух материалах при картировании EDS было очень близкое обнаружение. Тем не менее, диапазон обнаружения картирования EDS обычно может представлять глубину в микронном масштабе. Напротив, изображение BSD использовалось в качестве метода обнаружения топографии поверхности для получения более точной мезомасштабной информации.

В таблице 3 показана объемная доля каждого компонента на поверхности образца, основанная на подсчете характеристических значений, связанных с Si, SiC и графитом, в фазовом распределении набора данных после выделения признаков. Эти конкретные значения отличались от данных, наблюдаемых методом ЭДС. Поверхность образцов СГ-П-0,5 в основном состоит из графита, составляющего около 50 %, с 40 % SiC и 10 % свободной фазы Si. Поверхность образца LSI SiC в основном состоит из композита SiC, что указывает на объемное соотношение около 75%, около 20% графита и 5% свободного Si. Напротив, образец композитов LSI SiC содержал гораздо больше фаз SiC и меньше фаз Si на поверхности образца.
Доля фазового распределения на поверхности образца (об.%).
Составные части | СГ-П-0,5 | БИС SiC |
---|---|---|
карбид кремния | 40,66 | 74,28 |
графит | 49,45 | 21.46 |
Си | 9,89 | 4,26 |
Поскольку матрица обоих материалов была основана на графите, фаза Si может проникать во внутреннюю микроструктуру, в результате чего графит в ней проявлял форму замкнутого кристалла. Образец СГ-П-0,5 оценивается более чем в два раза больше по диаметру частиц графита в композите LSI SiC, так как разница увеличивается в размерах зерен графитов. Как правило, зерна графита в композитах LSI SiC имели диаметр несколько десятков микрометров с максимальным размером около 100 мкм. На поверхности образца СГ-П-0,5 размер зерен графита был значительно больше, диаметром от 100 до 250 мкм, причем зерна графита в основном были связаны друг с другом в матрице.
Рис. 8показывает изменение коэффициента трения во времени для различных образцов при различных нормальных нагрузках во время трибологических испытаний. Коэффициент трения образца СГ-П-0,5 в целом выше, чем у композита БСИ-SiC. В сухом состоянии коэффициент трения образца СГ-П-0,5 сначала повышается, а затем стабилизируется при трении. У образца СГ-П-0,5 значение КФ устойчивости составило 0,27 при нормальной нагрузке 10 Н, тогда как КФ был несколько выше, достигая 0,3 при нормальной нагрузке 40 Н. В водосмазываемом состоянии коэффициент трения образца СГ-П-0,5 уменьшался с увеличением продолжительности скольжения и в итоге стабилизировался на уровне 0,13 при нормальной нагрузке 10 Н и 0,12 при нормальной нагрузке 40 Н. COF композита LSI SiC был относительно чувствителен к нормальной нагрузке в сухом состоянии, где COF составлял 0,13 при нормальной нагрузке 10 Н и 0. 16 при нормальной нагрузке 40 Н. Кроме того, кривая коэффициента трения имела некоторую пилообразную форму.Рис. 8 б и г, где КФ внезапно повышался, а затем медленно возвращался к прежнему значению. При смазывании водой композит LSI SiC продемонстрировал очень низкий коэффициент трения 0,08 при нормальной нагрузке 10) и 0,09 при нормальной нагрузке 40 Н. Эти трибологические данные были аналогичны предыдущему отчету Zhou et al. [ 22 ], а трибологический механизм, связанный с этой эволюцией коэффициента трения

На рис. 9 показаны скорости износа при нормальной нагрузке 10 Н и 40 Н в сухом состоянии и в условиях смазывания водой. Стоит отметить, что скорость изнашивания образца СГ-П-0,5 уменьшалась с увеличением нагрузки. Наоборот, скорость износа композита LSI SiC увеличивалась с увеличением нагрузки. Оба материала обладают отличной износостойкостью в рабочих условиях. В водосмазываемом состоянии скорость изнашивания образца СГ-П-0,5 снижается. Скорость изнашивания композита LSI SiC значительно снизилась и составила всего 0,750× 10-5 мм 3 /Нм при нормальной нагрузке 10 Н при водяной смазке. Эти изменения показали, что композит БСИ SiC может иметь лучшую износостойкость при относительно меньшей нагрузочной способности, чем образец СГ-П-0,5.

Окислительный износ происходил на поверхности образца в сухом состоянии, где при трении фаза Si окислялась до SiO 2 , что свидетельствовало об обнаружении заметных царапин. Эти результаты согласуются с тем, что механизмы изнашивания тормозных материалов C/SiC в работе. . В водной среде не было явных следов износа, которые можно найти на поверхности двух материалов. Из табл. 2 можно сделать вывод , что вода может вступать в трибохимическую реакцию с поверхностью SiC. При трении на поверхностном слое может образовываться граничная пленка, приводящая к граничной смазке . Также выяснилось, что вода также может играть ключевую роль в рассеивании тепла, что может снизить температуру контактной поверхности для предотвращения реакций окисления. Реакция SiC и воды была следующей .
Следует отметить, что измерение толщины смазочной пленки может быть весьма проблематичным в эксперименте, выходящем за рамки этого объема. В данной работе можно сделать вывод, что формой смазки была граничная смазка, так как на поверхности трения при водяной смазке отсутствовала явная царапина, а коэффициент трения был значительно снижен. Кроме того, наблюдались внезапная нестабильность и повышение коэффициента трения , возникающие в процессе трения в композите LSI SiC, и одновременно наблюдались ямки на изношенной поверхности образца. Следует отметить, что частицы SiC полностью отличались от частиц графита. Это связано с тем, что твердость фазы SiC обычно была высокой (KH в 2960 кг/мм 2 ), тогда как спеченный SiC в жидкой фазе немного ниже, чем твердость спеченных материалов SiC в твердом состоянии, при этом демонстрируя высокую износостойкость. Следовательно, композит SiC может переходить в абразивные частицы после падения с изношенной поверхности образца и, следовательно, сосуществовать между двумя границами раздела в течение определенного периода времени. Поэтому абразивный износ может приводить к неустойчивому изменению в процессе трения. Объяснение вполне объяснимо тем, что скорость изнашивания SiC-композита БИС увеличивалась с увеличением нормальной нагрузки, тогда как у образца СГ-П-0,5 наблюдалось обратное изменение. Это также свидетельствует о том, что композит LSI SiC был более склонен к осыпанию зерен SiC во время трения. В условиях смазывания водой оба материала демонстрировали очень низкий коэффициент трения, в то время как состояние смазки вело себя как граничная смазка. В частности, не наблюдалось выпадения абразивных частиц, а поверхность композита LSI SiC характеризовалась низкой скоростью износа.
На рис. 6 неполированная поверхность композита LSI SiC наблюдалась с использованием увеличенного изображения SEM, и была обнаружена отчетливая зернистая микроструктура SiC. Согласно предыдущему исследованию Favre et al., он был преобразован в фазу β-SiC при изготовлении LSI, которая имеет характеристики очень высокой твердости и износостойкости одиночных зерен. Но кубическая структура зерен может легко вызвать концентрацию напряжений, когда эти зерна соприкасаются друг с другом. Когда поверхность образца подвергалась сильному напряжению при различных нормальных нагрузках, между зернами могут легко возникать некоторые трещины, что приводит к нарушению усталостного отслаивания . Морфология графита двух материалов сильно отличалась, основываясь на результатах выделения признаков для изображений BSE. По сравнению с образцом СГ-П-0,5 поверхность композита БСИ SiC содержала значительно больше SiC и меньше графита. Поэтому графит вел себя как замкнутые частицы на поверхности композита LSI SiC. На поверхности образца СГ-П-0,5 количество графита было значительно больше, а размер зерен значительно больше, чем на композите БСИ-SiC. В частности, размер зерен достигал диаметра 100–200 мкм, при этом большая часть частиц графита была связана друг с другом. Сила связи между ними была намного выше, чем в композитах LSI SiC.
В композите LSI SiC ямки отслаивания обычно появлялись на изношенной поверхности, а морфология внутри ямок была зернистой. Более того, поскольку отслоившиеся кристаллические зерна β-SiC обладали высокой твердостью, абразивный износ обычно происходил при трении. Именно по этой причине на рис. 8 произошло внезапное повышение коэффициента трения .. Вывод показал, что композит LSI SiC имеет более высокую скорость износа при высоких нагрузках. В образце СГ-П-0,5 зерна SiC были окружены графитовой фазой в матрице образца. Графит может выступать в качестве опорной микроструктуры и тем самым снижать концентрацию напряжений при трении. Поэтому не наблюдалось усталостного износа. Износ был получен в основном из-за графита с точки зрения наблюдения следов износа. Низкое межслойное усилие графита привело к хорошему эффекту смазки, что привело к низкому коэффициенту трения и скорости износа композита LSI SiC. Поскольку износостойкость графита была ниже, чем у фазы SiC, общая скорость изнашивания образца СГ-П-0,5 была несколько выше, но стабильные характеристики были лучше, чем во время испытания на трение.
Из-за взаимодействия между кристаллическими зернами осыпание графита при трении не было очевидным. Однако графит на поверхности композита LSI SiC действительно играет роль твердой смазки , и, следовательно, коэффициент трения был снижен. В будущем можно ожидать, что композит LSI SiC будет служить новым пористым материалом для подшипников качения и даже высокотемпературных подшипников с воздушной фольгой. Гибридный композит SiC/C также обладает самосмазывающимися свойствами, особенно для несмазочных керамических подшипников. Дальнейшим направлением исследований может быть сравнение ударной вязкости и ударопрочности гибридного композита SiC/C, а также поиск оптимальных условий микроструктуры кремний-графита для улучшения характеристик.
Трибологические эксперименты и выделение признаков были проведены на двух силицированных графитовых материалах: СГ-П-0,5 и композите LSI SiC. Образец СГ-П-0,5 имел КТР 0,26–0,3 при сухом трении , а КТР композита БСИ-SiC – 0,13–0,16. В условиях смазывания водой поверхность SiC образовывала граничную пленку, и, таким образом, состояние смазки было граничным , при этом коэффициент трения обоих материалов упал примерно до 0,1.
Тип изнашивания образца СГ-П-0,5 был преимущественно окислительным вместе с абразивным изнашиванием графита. Скорость изнашивания значительно уменьшилась, так как при трении увеличилась нормальная нагрузка. Основной тип износа композита LSI SiC также включает усталостный износ, который приводит к непрерывному падению зерен SiC. Вот почему коэффициент трения внезапно увеличился, а скорость износа увеличилась с ростом нормальной нагрузки. Окислительный износ поверхности в основном обусловлен реакцией окисления свободного Si при высокой температуре на границе раздела пар трения.
Доля фазы SiC составляла 75 % на поверхности образца LSI SiC. Между зернами карбида кремния при трении легко образовалась концентрация напряжений, что привело к расширению некоторых трещин и одновременному выпадению абразивных частиц, что в конечном итоге привело к возникновению абразивного износа. На поверхности образца СГ-П-0,5 преобладала графитовая фаза. Фаза SiC была окружена графитом в качестве структурной опоры для более высокой стабильности и усталостной долговечности .